生産性向上塾
2021年02月
2021.02.25
能率
計算式では、 標準時間/実績時間 と表される。
つまり、
1.0>であれば、「標準時間より、早く完了」となり、能率は高いことになり、
1.0<であれば、「標準時間より、遅く完了」となり、能率は低いことを示す。
但し、「標準時間」の見直しを定期的に行う必要があります。
やり方の見直し、特に「治工具」の進歩には目覚ましいものがあり、
「工夫された工具」が商品化されていることを知らずに、苦労することのないようにしたいものです。
また先般、分業の重要性で、「標準時間」の話の中で、「能率」をあげるために、
マニュアル、作業手順書等を作成することが(能力の底辺の底上げ)重要です。
但し、マニュアルの賞味期限は一般的に1年と言われます。
常に見直し、最新のもので作業に取り組みたいものです
手元にあるマニュアル・作業手順書(改訂履歴)が、1年以上前から同じものが使われているということは見直しがされていないということ。
そのやり方で、「工数」をかけていいのですか?「能率」は、上がるのですか?気づいた時が一番早い。見直しませんか?
2021.02.22
7つのムダ
ムダとは、付加価値を生まない作業をいいます。
人の動き(下記1~7の「 」部分)には、付加価値は生まなくても「必要な作業」と、それ自体「不必要な作業」があります。
一般的に言われている「7つのムダ」と解説は下記の通りです。
1. 「手待ち」のムダ | 機械故障、部品が来ないため、することがない |
---|---|
2. 「動作」のムダ | 要求されていること以外の動作をしない |
3. 「運搬」のムダ | 運搬、それ自体がムダ |
4. 「不良」のムダ | 不良・手直しは、生産効率・やる気を落とす |
5. 「在庫」のムダ | 在庫があるとその分、置き場が無くなる |
6. 「作り過ぎ」のムダ | 最も罪深いムダ |
7. 「仕事そのもの」のムダ | その仕事は(お客様にとって)必要? |
この中で、「不必要な作業」は「6作り過ぎ」「1手待ち」「4不良」が該当し、これらは全く以て不要です。
一方、「5在庫」「2動作」「3運搬」は、「必要な作業」です。但し、それ自体は「付加価値」を生まないため、最小限に抑えたい作業です。
では、「不必要な作業」を無くすために、
「必要な付加価値を生まない作業」を最小限にするためにどうしたらいいかを、下記に列挙します。
1. 手待ち(不必要) | 就業中に機械故障が起きないよう、日常点検を怠らないことです。 また工程間に手待ちがあるのであれば、作業手順(工程順)の見直しが必要かもしれません。 |
---|---|
2. 動作(必要) | 足を動かしても、付加価値は上がりません。 できるだけ動作の数を減らす工夫をしましょう。 |
3. 運搬(必要) | 但し、工場内の運搬距離は自分たちで決められます。工程間の運搬はゼロ化を目指しましょう。 |
4. 不良(不必要) | 表に出して情報共有しましょう。できれば限度見本を用い、「見える化」を進めましょう。 また、人のせいにせず、仕組みで解決しましょう。 |
5. 在庫(必要) | 在庫は置き場が必要になります。また、どの工程に在庫が必要かを見極めましょう。 但し在庫は、いくら管理しても収益は上がりません。削減する工夫が大切です。 |
6. 作り過ぎ(不必要) | 最も罪深いムダと言われています。製造原価(材料費・経費・人件費)を食うだけ。 安心代の裏返しです。 |
7. 仕事(必要) | その仕事って、お客様にとって必要?を考えましょう。 |
まずは、今やっている仕事を、見直しましょう。
その仕事(作業)は、「何のため(目的)にやっているのか」それが確認できれば、
あとは「やり方(手段)」になります。目的が明確になれば「必要」か 「不必要」かも明確になります。
2021.02.18
習熟の重要性
習うより、慣れろ。
習熟とは、そのことに充分に慣れ、上手になること。
たまに、こんな文句を言う人がいます。
「この仕事は、自分には向いていない」と。
}
残念ながら、このような人に「向いている仕事」はありません。何をやっても、同じです。
逆に、この仕事は、「この人にとって天職ですね」なんて言われる人もいます。
そんな人に、聞いてみると「向き、不向きよりも前向き」と笑顔で返ってきます。
どれだけその仕事を好きになろうとするかで、慣れるまでの時間も短くなり、色んな事が覚えられると。
慣れてくると、「工夫」出来るようになります。
やり方・道具の使い方・治具の改良等々これまでにない「付加価値」が得られるようになるかもしれません。
更に面白くなる段階です。
どんな仕事も、「工夫」ができるまではやりたいものです。
2021.02.18
研修受講者の声(11)原価の3要素

恥ずかしながら、QDCの内、Q(品質)やD(納期)については、日頃から上司にも言われてきましたので、部下にも厳しく言ってきましたが、数字の苦手意識もあり、「製造原価」については、全くの無関心でした。
当然、会社の利益について、考えて仕事をしていませんでした。
段取りの仕方で、こんなに利益が変わることを知りましたので、数字を出してみようと思います。
工場長 G様

原価の3要素「材料費・経費・人件費(労務費)」を出してみては如何でしょうか。
それぞれの内訳を概算で結構です。まずは、数字化してみることが大切です。
これまでは漠然と捉えていたものが、「数字」という共通語で議論できると、話の枠が広がります。
2021.02.15
分業の重要性
一般的には、仕事は、役割分担(適材適所)を決めたほうが、効率よくできる。 これを、分業という。
但し分業をしすぎる(「仕事」を細かく分けすぎる)と、単なる「作業」となってしまいます。
つまり仕事は「この人に是非」という思いがある一方、
作業は「誰でもできる」ものになってしまい、「やりがい」が得られないものになってしまいます。
仕事はその目的を明確にし、作業にならないようすべきです。
さて、 ここから先は特に仕事を「割り振る」方(リーダー等)のための話です。
「役割分担」は、ある意味「適材適所」にもつながる考え方でもあります。
下記確認ください。
概ね組織には、こんな3種類(仕事の時間の長さ)の人に分けられます。
標準時間のBさんを基準に、「手早いAさん」そして「手のろいCさん」 ということです。
さて各人の課題は、 手早いAさんは、組織の中では所謂「稼ぎ頭」です。
標準時間を上回る完成速度で仕上げていくことが出来るため、
複数の機械を担当するなどの多能工になって頂き、更に「稼働(可動)率」をアップさせるのに対して、
手のろいCさんは、標準時間を下回る時間でしか完成させることが出来ません。
よって、マニュアル等を利用して「能率」をアップさせることになります。
つまり標準(作業)時間を境に、課題が明らかに違うということです。
ところが多くの企業が、同じ組織にいるというだけで全員に同じ課題に取り組んでいる会社をよく見かけます。
その理由は「作業時間が見えていない」、つまり「感(勘)」で仕事をしているからです。
会社は組織で仕事をしています。
役割分担して分業することで仕事は効率化すると言いましたが、役割分担するには、まず作業者の力量を計測する必要があります。
その上で組織として、 それぞれの仕事を「誰が」「どのように(時間・やり方)」やるかを決めていきます。
そのための最初のステップが「標準作業時間(方法)」を知ることです。
標準作業時間(所要時間/やり方)が明確になっているからこそ、次なる課題が見えてきます。
手が早いAさんに該当するのは誰か、標準作業時間のBさんは誰か、手のろいC さんは誰か、
を見極めたうえで、目の前の課題を誰に担当してもらうかを決めるのが、本来の役割分担です。
2021.02.15
研修受講者の声(10)不具合・クレームが発生したときは…

不具合に関して、これまで個人を追及し始末書作成をさせること(手段に過ぎない)が一つの仕組みとなっており、
「目的」である再発防止が、二の次になっていたことに気付きました。
品質保証担当 F様

不具合・クレームの発生原因を追究し、仕組みを見直すことで「再発防止」に繋げましょう。
個人(他人)の責任にすることは責任を転嫁するだけで、再発防止にはなりません。
工程内に仕組みとして盛り込むことで、後工程に不良品が流れることが無くなります。
2021.02.08
5S(整理と整頓の違い)
日本語で、整理・整頓の違いを一言で言うなら
整理・・・捨てる
整頓・・・探さない
と、なろうかと。
もう少し、詳しく言うと、
【整理】要るものと、要らないものに分け、要らないものを捨てる
だから、大切なこと・・・まず、全部出すことです
【整頓】すぐ使える状態を保つ
なんてややこしく書かれているものもありますが、簡単に言えば「きれいに並べる」です。
つまり、見れば判る「3定(サンテイ)」が基本です。
定位・・・決められた位置に
定品・・・決められた品物を
定量・・・決められた量が
おかれていることです。
5Sには、必ず順番があります。
- 整理
- 整頓
- 清掃
- 清潔
- 躾
の順です。
決して、整頓・整理・・・ではありません。それぞれの意味は?
ちなみに5Sは英語では、このように訳されています
- 整理(Sorting:分ける)
- 整頓(Setting in Order:順に並べる)
- 清掃(Shining:磨く)
- 清潔(Standardizing:標準化)
- 躾 (Sustaining the Discipline:規律の維持)
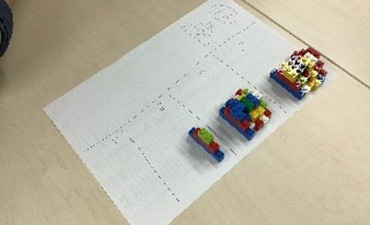
作業者にとって、「働きやすい環境」であることは、とても大切なことです。
「きれいな職場」は、働く皆さんが「きれいな職場」で、あり続けようとします。
そのために、「必要なもの」「要らないもの」が明確になり、それぞれの置き場もはっきりしています。
最近、掃除という言葉を「環境整備」に置き換えられています。
これは、仕事をするための環境を整えるという意味です。
そのために必要なこと、それが「整理」そして「整頓」です。
2021.02.08
研修受講者の声(9)製品の利益率を意識した設計業務

経営側の立場になって製品を作っていない事を認識しましたので、
製品の利益率について常に意識して設計業務を行いたいと思います。
設計担当 E様

設計はモノづくりの一番の上工程であり、原価の8割を決める部署です。
お客様の要求仕様(目的)を、図面への反映の仕方次第で、
後工程の製造現場(モノの調達・部品の加工・組立)での負荷量が大きく変わることにもなります。
設計「作業の標準化・部品の共通化」を進めることで、製造現場での「作業の平準化」を進めることが出来ます。
2021.02.04
準備・段取りの重要性
こんな諺(ことわざ)をご存知でしょうか?
段取り八分仕事二分
仕事をする前に、きちんとした「段取り」さえしておけば、仕事の8割がたは 終わったも同然ということです。
仕事にとりかかる前に、具体的に、仕事を進める手順を、きっちり 決めておけば、それだけ仕事の質とスピードは上がります。 これのことです。
2010年の研修受講当時、先生からは、 「モノづくりにとって段取りは、設計です」
如何にいい設計をするかで、製造の品質が決まりますとも教えて頂きました。
ここでも、「後工程はお客様」に繋がる話です。
尚、「モノづくり」の世界では準備と段取りは、微妙に違います。
準備+役割分担=段取り
つまり、事前にしなければいけないことを、順番に並べることを準備と言いますが、その準備の各項目を「誰が」やるのかもきめていることです。
さて、 フライス・旋盤・マシニングセンターを扱う方々にとって当たり前の言葉として、
使っている段取りには「外段取り」「内段取り」という言葉があります。
「外」段取りとは、生産を止めないで行う段取りのことで、
一方「内」段取りとは生産を止めて行う段取りのこと。
段取り時間には、「治具の交換」のみならず、「調整時間」も含まれます。
いずれも機械が停止状態(生産できない)を言います。
当然、機械の稼働時間が高い=生産金額アップに繋がるため、できるだけ、機械の稼働時間を高めるための「外段取り化」が、モノづくりにとって望ましい仕事のやり方です。
であれば当然のことながら、
機械加工作業者の脇には「段取り台車」(段取り替えを行う際に必要な刃具・治工具(セットされている台車のこと)があり、 組立作業者の脇には「工具台車」(組立作業に必要な工具類がセットされている台車)が機械の稼働率を高め、生産金額を高める重要なアイテムになります。
2021.02.04
研修受講者の声(8)顧客の欲しいものを如何に作るか

研修は、グループで議論し結論を出す方法で進められ、グループ討議の有効性を再認識、理解の深さも共有できました。またお金や納期の議論ばかりに注目し、顧客と距離が開いているのではないか、との部分に気づきを得られました。
B様

研修には、一社あたり、複数名で参加されることを希望します。
理由その1として、研修で学んだ成果を会社に戻ってカイゼン活動等で実行する際に仲間がいることで、一人でやるより進めやすくなります。
その2は、研修では、同一企業の方は違うグループで学んでもらいます。それによって、様々な考え方があることを知る機会が増えます。
例にあるように、自分の会社の考え方(常識)は他社では、通用しない(非常識)時もあります。
考え方の違いを知る機会にもなると思います。
釈迦に説法ですが、今は「いいものが売れる」のではなく、「売れるモノがいいもの」 作る側より、買う側(顧客)に主導権があります。
顧客の欲しいものを如何に作るかが 明暗を分けることになるのでしょう。
- 1 / 2
- 次のページ »